Die Cleaning (Extrusion Die Cleaning)
An ultrasonic cleaning machine cleans even the most demanding parts efficiently and saves working hours. Undoubtedly, ultrasonic cleaning has many advantages in industrial maintenance cleaning of production equipment
Conventional mechanical, manual cleaning of moulds, dies, extrusion tools and press tools is slow, labour intensive and sometimes abrasive and destructive to mould surface. Ultrasonic mould cleaning is based on a combination of chemical and mechanical cleaning to remove dry or wet contamination on metallic surfaces. It is gentle and non-abrasive to the base material. The cleaning takes place in immersion so no operator is required in the cleaning process.
Industry | Applications | Contamination |
---|---|---|
Plastic and rubber | Moulds | Oxides, gases, release agents, rubber and plastic residues, oil, scale |
Cold forming | Press tools | Metal debris, grease, oil, gall |
Casting foundries | Die cast moulds | Metal debris, oxides, carbon, grease, graphite |
Plastic and aluminium extrusion | Extrusion dies | Plastic, aluminium |
Glass moulding | Glass moulds | Grease, graphite |
Options for mould and die handling
A lifting beam or basket is used for supporting the mould and die parts during the washing process. Tanks are equipped with support bars that are compatible with both the lifting beam and basket, and allow detaching the hoist and closing the tank lid for the duration of the cleaning.
Chain Hoist
- Compatible with the cleaning line
- Ergonomic load handling
- A ready-to-use floor fitted chain hoist makes the purchasing and installation a straight forward process.
- The complete system is CE marked.
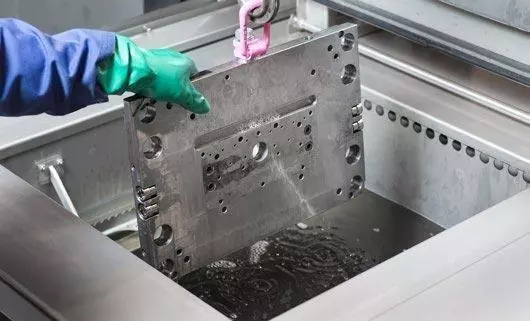
Lifting beam for mould plates
- The mould is hung on the beam with shackles.
- A matching interface for the support bars in the tank.
- One point lifting for convenient handling with a chain hoist
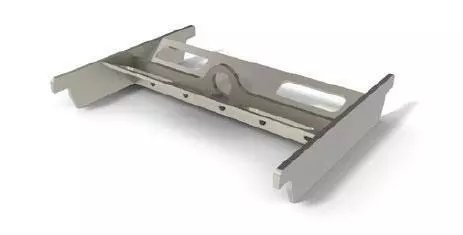
Basket for mould and die plates / parts
- The mould or die is hung on the beam with shackles.
- A matching interface for the support bars in the tank.
- One point lifting for convenient handling with a chain hoist
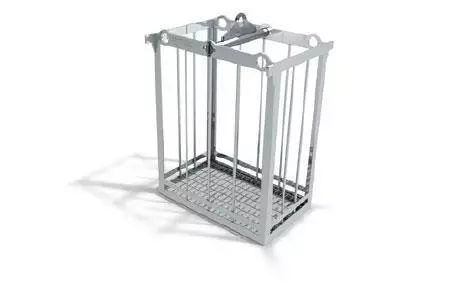
Ergo Station
Ergo Station is an innovation for the manual rinsing, flushing, drying and inspection of die and moulds. Its main advantages include a high level of safety and ergonomics thanks to a fully enclosed, brightly lit and ventilated working chamber. Operating the machine is safe and easy as parts are loaded through a sliding side door and supported with a hoist during the treatment.
Die cleaning process
- Ultrasonic wash at 80°C for about 5-15 minutes
- Rinsing with air bubble agitation for about 1 minute
Optional
- Preservation with dewatering or hot passivation for about 1 minute
- Inspection / manual intervention
Cleaning Aluminum Extrusion - Case Study
Material: Aluminum
Component: Extrusion
Contamination prior to cleaning: Machine debris, light surface commination
Ultrasonic Cleaner | Cleaning Fluid | Temperature(s) | Concentration |
---|---|---|---|
Versa Genius+ 120 Ultrasonic cleaner 30 KHz | Galvex 20.02 | 55°C | 3% |
Versa Genius+ 120 air bubble rinse | Tap water | 22°C | 100% |
Versa 120 Genius+ Hot air dryer | N/A | 70°C | N/A |
Process for cleaning Extrusion:
Stage 1- Galvex 20.02: Galvex 20.02 is a light alkaline liquid, used for the removal of polishing compounds in ultrasonic or soaking processes. It is compatible with all metals except carbides and can be easily rinsed leaving a bright & spot-free finish. It offers complete removal of polishing compounds, light oils, grinding oils and fingerprints and is highly efficient on brushed, satin and stippled parts (complex geometry). The tank was initially filled with tap water, then diluted with a 3% concentration of Galvex 20.02 and allowed to reach the required temperature of 55°C. The component was placed vertically in the basket and cleaned in the ultrasonic for 5 minutes.
Stage 2 – Tap water rinse: Next, the part was rinsed for 2 minutes in tap water using the air bubble agitation feature. The air bubble agitation feature Increases the efficiency of immersion rinsing. The treatment timer controls air bubble agitation via a solenoid valve. The auto purge feature was also used to wash away Galvex 20.02 detergent carry over. The auto purge feature adds fresh water automatically in conjunction with treatment cycle by opening a solenoid valve. Excess water is led to drain through overflow weir. Without this feature the tank would quickly become polluted and would need to be drained, cleaned & refilled to ensure rinse water quality is kept high.
Stage 3 – Hot air dryer: The part was then dried for 5 minutes at 70°C in the hot air dryer. Upon inspection the results looked good, the internal channels are now free from debris and oil, and the external aluminium extrusion appears brighter. The remaining 3 parts were then cleaned as a batch with the same process time and parameters as above.
Results: Visually good with no signs of any lapping residue and no oxidation.